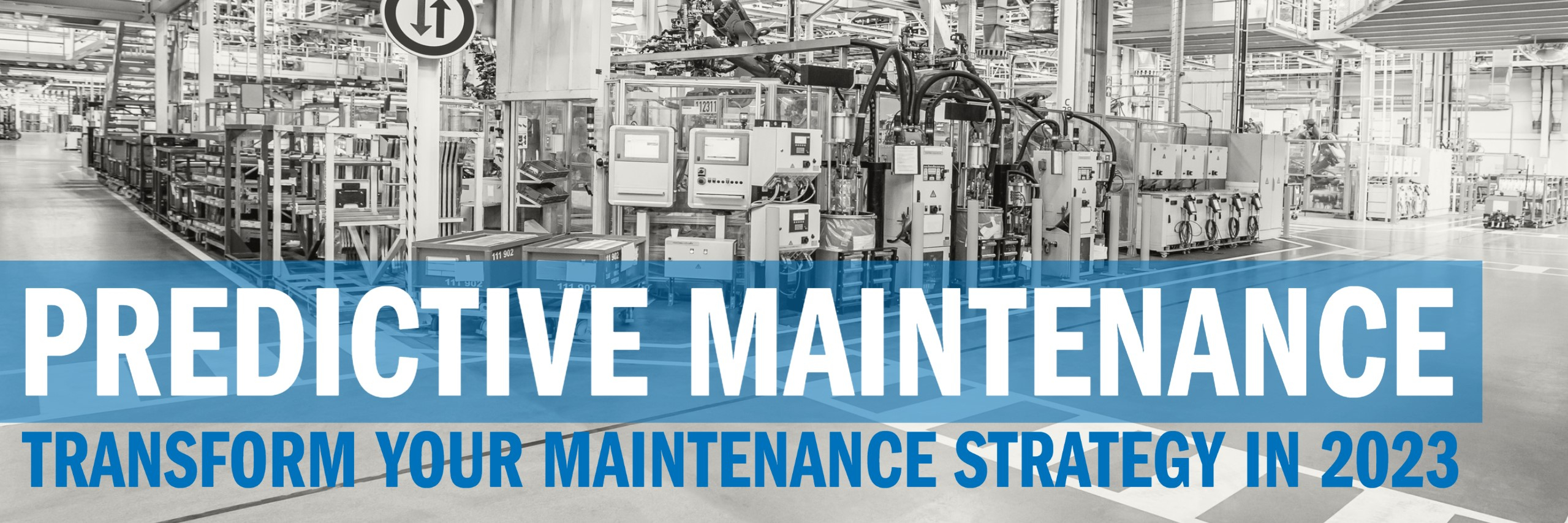
Introduction to Predictive Maintenance
In conjunction with Omron Industrial Automation
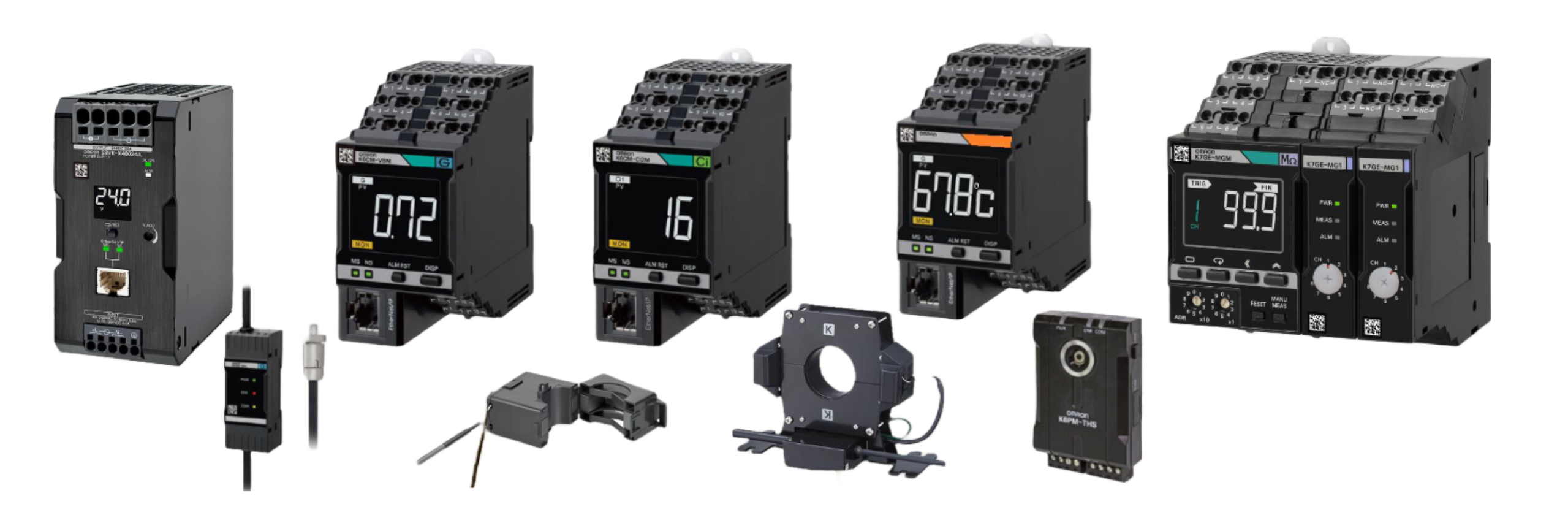
Looking at ways to transform your maintenance strategy?
This week we talk about Predictive Maintenance and how implementing IoT equipment to monitor and analyse your applications in real time can save you time and money.
What is predictive maintenance?
Predictive maintenance is the key to reducing unwanted downtime and operational costs. It is a type of maintenance that directly tracks your application or equipment’s health, status, and performance in real time. Predictive maintenance solutions help reduce cost, unexpected breakdowns and offers the manufacturer the opportunity to plan maintenance around their own production schedule.
These innovative solutions help predict equipment deterioration, misalignment, or imbalance without the need for manual intervention.
5 advantages of predictive maintenance
Predictive maintenance is a transformative application of the IIoT with huge advantages. Below, we explore five benefits that can serve as differentiators for your organisation:
Decreased downtime
Predictive maintenance enables technicians to detect issues in advance and resolve problems before equipment failure can occur, so you can:
- Cut unplanned downtime
- Schedule multiple service procedures at one time
- Avoid the risk of reputation-damaging outages
- Reduce costly technician call outs required by unexpected downtime
Increased worker productivity
The need to disrupt workers productivity due to unexpected malfunction are eliminated. Predictive maintenance plans around workers’ schedules, and helps to:
- Speed up service time-to-resolution
- Maximizes uptime and prevents productivity lags
Reduced field service costs
By anticipating machine maintenance, service departments can generate major cost-savings and increased ROI through:
- Reduction of costly service call outs
- Increased first-time fix rates
- Streamlined maintenance costs through reduced labour, equipment, and inventory costs
Improved Product Design
Harnessing the power of IIoT data collected through your machine’s monitoring solutions, product designers can use this vital information to:
- Extend asset lifespans
- Improve equipment durability and reliability
- Build more efficient machines in the future
Improved worker safety
An unexpected breakdown or malfunction may lead to hazardous working conditions for your employees. By predicting when a malfunction may occur, you can ensure:
- Technicians can carry out service before a machine becomes dangerous
Implementing predictive maintenance to existing equipment
Production facilities and equipment are built without waste and optimised for each user by equipment and panel manufacturers. Therefore, adding a new function to such facilities requires extensive renovation and construction work, which require a lot of labour and cost.
In addition, for production lines that are required to be always available so as not to lose any opportunity, major modifications such as this, which may affect existing functions, make companies think twice about implementing predictive maintenance.
Accordingly, condition monitoring devices are designed to enable retrofitting to simplify the addition of functions to existing equipment. Devices are designed to minimize the labour required by maintenance personnel for installation, verification, design, and operation associated with the addition of new functions. This is not just a retrofit function, but also a design that is closely aligned with the activities of the maintenance personnel who are responsible for the important task of maintenance.
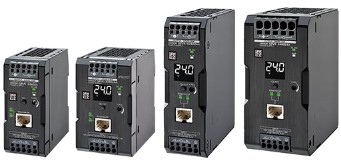
Ideas for updating maintenance strategies in water processing applications
Omron has released a white paper that talks about implementing smart maintenance solutions for the water industry and this is a great example of how predictive maintenance solutions can help keep your operations running smoothly.
Read it here >>>